Red 3 5.1 Surround Compressor/Limiter
- Main Inputs and Outputs are transformer balanced.
- Compressor and Limiter Threshold are 11 position rotary switches.
- Compressor Ratio is 12 position rotary switch selecting 1.3, 1.4, 1.5, 1.75, 2, 2.5, 3, 3.5, 4, 5, 7 & 10 to 1 ratios.
- 80, 100, & 120Hz selectable hi-pass for side chain.
- 80, 100, & 120Hz selectable lo-pass for Sub Channel.
– A client called me one day to ask about something they saw on the internet. They read an article which described how Focusrite built a Surround Compressor for Tori Amos. The client wanted to know more about it and could I build one for them. After a few phone calls to Focusrite UK, I finally determined that they had connected the side chain of two of their Red 3 compressors together to make a 4 channel compressor which was being used for a surround mix. Focusrite was kind enough to send me the “hand drawn” notes of their work, but after much discussion with the client, the two of us determined that it was not exactly what they wanted. So after many months of phone calls, letters, emails and drawings we began to formulate a plan.
– Basically we would use three Red 3’s so we could control each channel of a 5.1 mix (Left, Right, L Surround, R Surround, Center, and Sub), and link the side chains so that they would compress and track together. Of course as the client began to find and purchase the Red 3’s, more and more details were added. The client wanted all the Red 3’s to have input transformers as well as output transformers and to replace all the threshold and ratio pots with rotary switches so that all settings could be recalled and set exactly between units. During those early stages of discussion, we determined that we would go even further than Focusrite by linking not only the compressor’s side chains but also link the limiter’s side chains as well. We determined that the only way to control all these units would be from an external panel so that an operator could “enable/disable” the desired channel from the 5.1 bus. We felt it would work like the “Stereo” button on a single Red 3, so that when you “enabled” the channel to the 5.1 bus, the LED indicators and controls for that channel would shut off because it was controlled from the master channel, which in this case would be the Center channel. Since we were going this far we felt that we should add selectable Hi Pass filters of 80, 100, and 120Hz to side chain to prevent the Sub channel from “pumping” the other channels. And finally since the Sub channel was only going to control low frequencies, a selectable Lo Pass filter of 80, 100, and 120Hz would be added to the actual audio path to keep anything else from effecting the Sub channel’s action.
– A significant guideline that we imposed on this project was that ALL of the Red 3’s had to perform normally when not “enabled” or unplugged from each other and we would not alter any of the Red 3’s in a permanent way by drilling ANY holes in their beautiful red anodizied aluminum chassis or polished stainless steel covers.
– The project was finally completed in 2007 and shipped to the client. However the client decided that after changing the Ratio pot to the old style Red 3 rotary switch, that 6 fixed compression ratios were not enough. So the entire unit was sent back to us in 2008 to modify the Ratio switch to 12 positions. At that time we also moved the D-sub link connector from the top of each unit to the back so the units could be racked on top of each other without any wasted rack space. Having just completed these additions and shipping the completed unit back to the client, I thought it would be a great time to show you just what we did to create this incredible functioning, amazing sounding, 5.1 surround compressor/limiter.
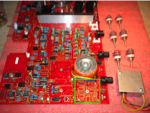
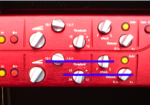
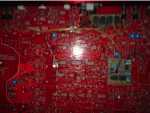
– Now that we had three fully transformer balanced, rotary switched Red 3’s done we were faced with the task of linking them all together so they would compress and limit as one unit. As you can see in the picture at the left this would require quite a few “trace cuts”, added wires and relays. Rather than taxing each Red 3 ‘s power supply to power the added relays we decided to run their power from an external supply located on our “add on” control panel. The relays were all wired so that in their “normally opened” position each Red 3 would be stock. However we did run the audio IC’s which were built on small “daughter” boards to house the additional electronics, from each Red 3’s power supply in order not to compromise the grounding system of each unit. To ensure the audio quality would be the same as an original Red 3 we used the exact relays and IC’s that Focusrite used in our add on “daughter” boards. In the picture on the right you can see the switchable filters that were added and mounted above/below the input transformers utilizing the input transformers’ mounting hardware.
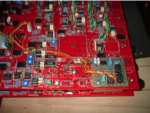
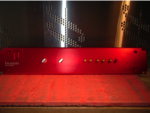
– In keeping with this extraordinary project, a simple aluminum rack panel would never do for a control panel. Having remembered that Focusrite once produced a 2U blank panel with the same aesthetics of the Red Series line, another call to the UK produced the “Red 0 Rack Enhancer”. This was the panel we used to house our master controls for all three Red 3 units. We machined the Red 0 to fit the same EAO and Grayhill switches used on the Red 3’s.
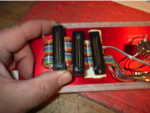
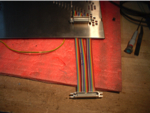
– Next, we needed 20 plus wires to link the units. We decided to use 25 pin D sub connectors to connect the units together. Originally on each Red 3’s top cover we mounted a 25 pin female D sub connector with the wires running through the existing holes on the stainless cover. This was done to avoid drilling any holes into the back panel and so when the three Red 3’s were installed in a rack there would be “air space” between them. The “air space” also prevented magnetic fields from each of the three power transformers interfering with the adjacent units’ sensitive VCA. This was changed two years later in 2009. (see below) Once the control panel was completed and tested, it was disassembled and sent to be laser engraved with lettering as close a match as we could get to the original Focusrite lettering on the Red 3’s.
– Well after a years worth of planning, designing, obtaining the units, searching for parts, modifying PCB’s and then finally connecting it all up… we were done. We had tested and calibrated it throughly in our shop but felt that it really needed to be tested in the real world with a real 5.1 audio mix running through it. So we enlisted the help of our friends at Studio at the Palms, here in Las Vegas. After patching it in to their console’s output via their patchbay we were finally treated to a 5.1 surround mix compressed and limited via the new Focusrite Red 3 5.1 Surround Compressor/Limiter. Truly impressive ! That crisp clean pristine uncolored Focusrite sound combined with the ultimate in 5.1 surround flexibility made listening to the mix a real pleasure. In the end we actually had a hard time prying the unit of of the studios’ hands so that we could pack and ship it to it’s new owner.
– Our client after receiving the 5.1 Red 3 Compressor/Limiter once again began to question us regarding its functionality. If the PCB could fit the 12 way rotary switch used for the Ratio, and the front panel had room for it, why did we limit it to the 6 ratios that the original Red 3 had? The plan was simple, they would obtain another Red 3, we would outfit it with transformers, obtain another “switched” Red 3 front panel from Focusrite and then modify the Ratio switch to have 12 ratios. While we set about doing all the preliminary work, i.e. obtaining all the proper parts, the client went about deciding the exact ratios that they would like to see on this unit. After receiving the list of ratios, I set up a spread sheet to help select the proper resistors to give me the exact voltage I would need to make the sidechain react exactly to the ratios chosen. Since they actually add up in value the resistors would have to be precise to give me the exact outcome I expected. A couple values were not even in the scope of 1% resistors so a few would have to be series/paralleled to result in the value required. The picture at the right shows how we had the lettering laser engraved around the switch. Because you cannot erase the old lettering, the old 10:1 position is actually 4:1, while the old 1.5:1 position is actually just that 1.5:1. Once again calibrated, tested, packed and shipped, the newly modified Red 3 was on it’s way to our client.
– So of course our client after receiving the 12 position Ratio Red 3 Compressor/Limiter realized that his 5.1 Surround Red 3 system was now incomplete. The client then boxed up all three of his other Red 3’s and sent them back to us along with the control panel and cables. Now our plan was this: add the 12 position Ratio switch to all three units and move the link connector to the back panel so that they could be racked up without any space between them. The client was aware of the sensitive VCA’s and planned on installing a mu metal shield between them if shielding proved to be an issue. So now we had to completely disassemble each unit so that we could have the front panels sent off to be laser engraved. At this time we made some minor corrections from the other Red 3 control panel: the numbers that were to the right of the decimal point needed to be in a smaller font to match the original 1.5:1 that was already lettered on the panels. And the 2:1 position should have read 2 instead of 2.0. If you look closely at the pictures above you will see the difference.
– As for moving the 25 pin D sub connector to the back panel, I did not want to drill and machine through the red anodized back panel. Ultimately I came up with the idea to run the cabling through the 0dB/-6dB internal operating level hole and mount the connector to one of the screws on the XLR output connector. This left the back panel untouched so the units could be returned to their stock condition if need be. Of course this didn’t make our job any easier as we still had to unwire each 25 pin D sub from the top cover, thread the wire through the back panel and rewire it there. In the end I carefully checked out each and every ratio position to insure all 3 units were exactly the same. And finally every switch, knob and light was tested to make sure we got them all put back together again properly.
– Now this may really be the end of this project. Unless of course the client starts talking about 7.1 surround…
– I want to thank all the people over the years who were responsible for making this happen.
Mick A’Court of Focusrite UK – without Mick’s tendencies of “stashing away” good parts to be used someday, this project would have never got as far as it did. Mick literally scrounged around all the piles of scrap that Focusrite had to get us the last input transformers and “switched” Red 3 panels they had. Cheers Mick !
Tom Schlum of Capitol Studios, Hollywood – Tom is the real person responsible for making these 3 units work together as one system. No matter how much both the client and I threw at him he shrugged it off and said OK I’ll give it a try. Without his expertise I’m not sure I would have tackled such a job. Thanks Tom !
Erika Earl of Thermal Relief Design – Erika, despite not having a clue to what I was up to, managed to read my mind and cut and link traces like a pro. Without her help our client would be waiting another year for me to complete this project. Thank you Erika !
Bob Ferra of Lex Products – Bob had to laser engrave the panels despite never working with this material and trying hard to match what we wanted with all “napkin” sketches we gave him. Thanks Bob !
And finally the biggest credit and thanks goes to our client August Martin of PRN-PRO, whose vision of this project was unstoppable. August always knew what he wanted and molded us all to get it. Thank you for your knowledge, perseverance, and patience August !
– Tony Marra Feb. 07 2009